Ливење под притиском
Калупно ливење је поступак ливења метала који се одликује убризгавањем растопљеног метала под високим притиском у шупљину калупа. Шупљина калупа је створена помоћу две каљене матрице за алатни челик, које су обрађене у подесном облику и раде слично калупу за убризгавање током процеса. Већина ливених одливака израђена је од обојених метала, посебно цинка, бакра, алуминијума, магнезијума, олова, пјутера и легура на бази калаја. У зависности од врсте метала који се лије, користи се машина са топлом или хладном комором.
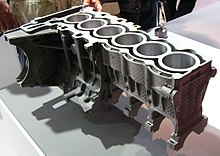
Опрема за ливење и метални калупи представљају велике капиталне трошкове, што ограничава поступак на велико-количинску производњу. Израда делова помоћу ливења под притиском релативно је једноставна, и обухвата само четири главна корака, чиме се ограничавају трошкови по комаду. Она је посебно погодна за велику количину одливака мале до средње величине, због чега се ливењем под притиском добија више одливака од било ког другог поступка ливења.[1] Лив под притиском одликује се врло добром завршном обрадом површине (према стандардима за ливење) и конзистентношћу димензија.
Историја
уредиОпрема за ливење под притиском изумљена је 1838. године у сврху производње покретних типова за штампарску индустрију. Први патент који се односи на ливење под притиском додељен је 1849. године за малу машину са ручним погоном у сврху механизоване производње штампе. Године 1885, Ото Мергенталер је изумео машину за линотип, која је изливала читаву линију типова као једну целину, користећи поступак ливења под притиском. То је готово у потпуности заменио ручно подешавање у издавачкој индустрији. Сосова машина за ливење под притиском, произведена у Бруклину у држави Њујорк, била је прва машина која се продавала на отвореном тржишту Северне Америке.[2] Остали видови примене су брзо напредовали, при чему је ливењем под притиском олакшавало раст робе широке потрошње и уређаја, у великој мери смањујући производне трошкове комплексних делова у великим количинама.[3] Године 1966,[4] Генерал Моторс је објавио процес Акурад.[5]
Ливни метал
уредиГлавне легуре за ливење под притиском су: цинк, алуминијум, магнезијум, бакар, олово и калај; мада је необичајено ливење гвожђе оксида под притиском је исто тако могуће.[6] Специфичне легуре за ливење под притиском укључују: цинк алуминијум; алуминијум, нпр. стандарди алуминијумске асоцијације (АА): АА 380, АА 384, АА 386, АА 390; и АЗ91Д магнезијум.[7] Следи сажетак предности појединих легура:[8]
- Цинк: метал најлакши за ливење; има високу дуктилност; има велику ударну чврстоћу; лако је обложен; економичан је за мале делове; промовише дуготрајан одливак.
- Алуминијум: лаган; иаа високодимензионална стабилност за врло сложене облике и танке зидове; поседује добру отпорност на корозију; има добре механичке особине; има високу топлотну и електричну проводљивост; задржава чврстоћу на високим температурама.
- Магнезијум: метал најлакши за обраду; има одличан однос чврстоће и тежине; ово је најлакша легура у широкој употреби за ливење.
- Бакар: велика тврдоћа; висока отпорност на корозију; највиша механичка својства ливених легура; одлична отпорност на хабање; одлична стабилност димензија; његова снага се приближава снази челичних делова.
- Силицијумски томбак: легура високе чврстоће која се састоји од бакра, цинка и силицијума. Ова легура се често користи као алтернатива за ливене челичне делове.
- Олово и калај: велика густина; изузетно блиска прецизност димензија; користи се за посебне форме отпорности на корозију. Такве се легуре не користе у прехрамбеним применама зарад јавног здравља. Типски метал, легура олова, калаја и антимона (са понегде и траговима бакра) користи се за ливење ручно постављаног типа у високопритисној штампи и блокирању врућом фолијом. Традиционално ливење у калупима је сада углавном замењено ливењем под притиском након индустријализације ливница. Око 1900. године машине за ливење штампарких компоненти појавиле су се на тржишту и допринеле даљој аутоматизацији, са понекад десетинама машина за ливење у једном новинском уреду.
Максимално ограничење тежине за одливке од алуминијума, месинга, магнезијума и цинка су приближно 70 лб (32 кг), 10 лб (4,5 кг), 44 лб (20 кг), и 75 лб (34 кг), респективно.[9]
Коришћени материјал дефинише минималну дебљину пресека и минимални газ потребан за ливење, како је наведено у доњој табели. Најдебљи пресек треба да буде мањи од 13 мм (0,5 ин), али може бити и већи.[10]
Метал | Минимални пресек | Минимални газ |
---|---|---|
Алуминијумске легуре | 0,89 мм (0,035 ин) | 1:100 (0,6°) |
Месинг и бронза | 1,27 мм (0,050 ин) | 1:80 (0,7°) |
Магнезијумске легуре | 1,27 мм (0,050 ин) | 1:100 (0,6°) |
Цинкове легуре | 0,63 мм (0,025 ин) | 1:200 (0,3°) |
Процес
уредиСледе четири корака у традиционалном ливењу под притиском, такође познатом као ливење под високим притиском,[5] они су такође основа за било коју од варијација ливења под притиском: припрема калупа, пуњење, избацивање и истресање. Матрице се припремају прскањем шупљине калупа мазивом. Мазиво помаже у контроли температуре матрице и такође помаже у уклањању одливака. Матрице се затим затварају и растопљени метал се убризгава у калупе под високим притиском; између 10 и 175 МПа (1.500 и 25.400 пси). Када се шупљина калупа напуни, притисак се одржава све док се одливак не очврсне. Матрице се затим отварају и артикал (они се разликују од одливака јер у калупу може бити више шупљина, што даје више одливака по операцији) се избацује помоћу клинова за избацивање. Коначно, истресање укључује одвајање отпада, који укључује капију, клизаче, отворе и блиц, од одливања. Ово се често ради помоћу посебне матрице за обрезивање у електричној или хидрауличној преси. Друге методе истресања укључују тестерисање и млевење. Мање радно интензиван метод су ударци превртања ако су капије танке и лако се ломе; мора уследити одвајање капија од готових делова. Овај отпад се рециклира претапањем.[11] Принос је приближно 67%.[12]
Инспекција
уредиНакон истресања одливака он се прегледа за недостатке. Најчешћи кварови су погрешно покретање и хладно затварање. Ови дефекти могу бити узроковани хладним калупима, ниском температуром метала, прљавим металом, недостатком вентилације или вишком мазива. Други могући недостаци су порозност гаса, порозност скупљања, вруће сузе и трагови протока. Ознаке протока су трагови остављени на површини одливака због лошег затварања, оштрих углова или прекомерног мазива.[13]
Предности
уредиПредности ливења под притиском:[10]
- Одлична тачност димензија (зависи од материјала за ливење, али обично 0,1 мм за првих 2,5 цм (0,004 инча за први инч) и 0,02 мм за сваки додатни центиметар (0,002 инча за сваки додатни инч).
- Глатке ливене површине (Ра 1—2,5 µм или 0,04–0,10 тхоу рмс).
- Тањи зидови се могу лити у поређењу са ливењем у песак и трајним калупима (приближно 0,75 мм или 0,030 ин).
- Уметци могу бити ливени (као што су уметци са навојем, грејни елементи и носеће површине високе чврстоће).
- Смањује или елиминише секундарне операције обраде.
- Брзе стопе производње.
- Затезна чврстоћа ливења до 415 МПа (60 кси).
- На дужину течности за ливење под притиском не утиче опсег очвршћавања, за разлику од трајних калупа, одливака у песку и других типова.[14]
- Стопе корозије за ливење под притиском су спорије од оних за ливење у песку због глађе површине одливака под притиском.[15]
Недостаци
уредиГлавни недостатак ливења под притиском је веома висок капитални трошак. Потребна опрема за ливење, калупи и повезане компоненте су веома скупи, у поређењу са већином других процеса ливења. Стога, да би ливење под притиском био економичан процес, потребан је велики обим производње. Остали недостаци су:
- Процес је ограничен на метале високе флуидности. Повећане стопе отпада могу бити узроковане поремећајима флуидности, и трошкови отпада у ливењу под притиском су високи.[16]
- Ливење под притиском укључује велики број делова, тако да су питања поновљивости посебно важна.[17]
- Тежина одливака је раније била ограничена на између 30 грама (1 оз) и 10 кг (20 лб),[ноте 1][10] али су од 2018. године постали могући ударци од 80 кг (180 лб).[18]
- У стандардном процесу ливења под притиском, коначни одливак ће имати малу количину порозности. Ово спречава било какву топлотну обраду или заваривање, јер топлота изазива ширење гаса у порама, што узрокује микро-пукотине унутар дела и љуштење површине. Међутим, неке компаније су пронашле начине да смање порозност дела, дозвољавајући ограничено заваривање и топлотну обраду.[4] Стога је сродни недостатак ливења под притиском то што је подесно само за делове у којима је мекоћа прихватљива. Делови којима је потребно отврђавање (кроз каљење или отпуштање) се не лију под притиском.
Нотес
уреди- ^ Дие цастинг ис ан ецономицал алтернативе фор ас феw ас 2,000 партс иф ит елиминатес еxтенсиве сецондарy мацхининг анд сурфаце финисхинг.
Референце
уреди- ^ „Дие Цастинг вс Отхер Процессес” (на језику: енглески). Архивирано из оригинала 23. 09. 2016. г. Приступљено 16. 9. 2016.
- ^ Мацхинерy'с референце сериес, Тхе Индустриал Пресс, 1913, Приступљено 18. 11. 2013.
- ^ Абоут дие цастинг, Тхе Нортх Америцан Дие Цастинг Ассоциатион, Архивирано из оригинала 21. 10. 2010. г., Приступљено 15. 10. 2010.
- ^ а б Лиу, Wен-Хаи (8. 10. 2009), Тхе Прогресс анд Трендс оф Дие Цастинг Процесс анд Апплицатион, Архивирано из оригинала 14. 3. 2012. г., Приступљено 19. 10. 2010.
- ^ а б Јохн L., Јорстад (септембар 2006), „Алуминум Футуре Тецхнологy ин Дие Цастинг” (ПДФ), Дие Цастинг Енгинееринг: 18—25, Архивирано из оригинала (ПДФ) 14. 6. 2011. г..
- ^ Дегармо, стр. 328
- ^ Дие Цастинг, ефунда Инц, Приступљено 12. 4. 2008.
- ^ ФАQ Абоут Дие Цастинг, Архивирано из оригинала 21. 10. 2010. г., Приступљено 12. 4. 2008.
- ^ Аллоy Пропертиес, Тхе Нортх Америцан Дие Цастинг Ассоциатион, Архивирано из оригинала 6. 6. 2013. г., Приступљено 12. 4. 2008.
- ^ а б в Дегармо, стр. 331
- ^ Дегармо, пп. 329-330.
- ^ Бревицк, Јералд; Моунт-Цампбелл, Цларк; Моблеy, Царролл (2004-03-15), Енергy Цонсумптион оф Дие Цастинг Оператионс (ПДФ), Охио Стате Университy, дои:10.2172/822409, (УС Департмент оф Енергy Грант/Цонтрацт Но. ДЕ-ФЦ07-00ИД13843, ОСУРФ Пројецт Но. 739022), Приступљено 2010-10-15.
- ^ Аведесиан, M. M.; Бакер, Хугх; АСМ Интернатионал (1999), Магнесиум анд магнесиум аллоyс (2нд изд.), АСМ Интернатионал, стр. 76, ИСБН 978-0-87170-657-7
- ^ Хан, Q.; Х., Xу. „Флуидитy оф аллоyс ундер хигх прессуре дие цастинг цондитионс”. Сцрипта Материалиа. 2005. 53(1): 7—10.
- ^ „Дие Цастинг”. форцебеyонд.цом. Архивирано из оригинала 2019-02-27. г. Приступљено 2021-06-03.
- ^ Деwхирст, Б. „Цастабилитy Меасурес фор Диецастинг Аллоyс: Флуидитy, Хот Теаринг, анд Дие Солдеринг”. Процеедингс оф тхе 4тх Интернатионал Хигх Тецх дие Цастинг Цонференце — преко ХТДЦ. 2008.
- ^ „Цастабилитy Цонтрол ин Метал Цастинг виа Флуидитy Меасурес: Апплицатион оф Еррор Аналyсис то Вариатионс ин Флуидитy Тестинг” (ПДФ). wеб.wпи.еду. Архивирано (ПДФ) из оригинала 2021-06-03. г. Приступљено 2021-06-03.
- ^ „Идра интродуцес тхе wорлд'с ларгест дие цаст мацхине”. Асосиаси Италиа Пемасок Фоундриес. 2018-02-01. Архивирано из оригинала 19. 04. 2021. г. Приступљено 2020-04-20. „цапабле то продуце цастингс wелл беyонд 80 кгс ин wеигхт овер ан унбеатен маxимум аллоwед пројецтед ареа. … мануфацтуре оф хигх-интегритy Алуминиум анд Магнесиум Дие Цаст цомпонентс фор тхе аутомотиве сецтор, wитх фоцус он струцтурал анд сафетy цритицал цомпонентс. … Ињецтион велоцитy еxцеединг реqуирементс оф 10 м/сец”
Литература
уреди- Давис, Ј. (1995), Тоол Материалс, Материалс Парк: АСМ Интернатионал, ИСБН 978-0-87170-545-7.
- Дегармо, Е. Паул; Блацк, Ј Т.; Кохсер, Роналд А. (2003), Материалс анд Процессес ин Мануфацтуринг (9тх изд.), Wилеy, ИСБН 0-471-65653-4.
- Андресен, Билл (2005), Дие Цастинг Енгинееринг, Неw Yорк: Марцел Деккер, ИСБН 978-0-8247-5935-3.
- Блаир, Малцолм; Стевенс, Тхомас L. (1995), Стеел цастингс хандбоок (6тх изд.), АСМ Интернатионал, ИСБН 978-0-87170-556-3.
- Дегармо, Е. Паул; Блацк, Ј Т.; Кохсер, Роналд А. (2003), Материалс анд Процессес ин Мануфацтуринг (9тх изд.), Wилеy, ИСБН 0-471-65653-4.
- Калпакјиан, Серопе; Сцхмид, Стевен (2006), Мануфацтуринг Енгинееринг анд Тецхнологy (5тх изд.), Пеарсон, ИСБН 0-13-148965-8.
- Кисселл, Ј. Рандолпх; Феррy, Роберт L. (2002), Алуминум струцтурес: а гуиде то тхеир специфицатионс анд десигн (2нд изд.), Јохн Wилеy анд Сонс, ИСБН 978-0-471-01965-7.
- Сцхлег, Фредерицк П.; Кохлофф, Фредерицк Х.; Сyлвиа, Ј. Герин; Америцан Фоундрy Социетy (2003), Тецхнологy оф Металцастинг, Америцан Фоундрy Социетy, ИСБН 978-0-87433-257-5.
- Стефанесцу, Дору Мицхаел (2008), Сциенце анд Енгинееринг оф Цастинг Солидифицатион (2нд изд.), Спрингер, ИСБН 978-0-387-74609-8.
- Рави, Б (2010), Метал Цастинг: Цомпутер-аидед Десигн анд Аналyсис (1ст изд.), ПХИ, ИСБН 81-203-2726-8.